Executive Philosophy: Take immediate action and be meticulous.
Development Philosophy: first-class enterprise, first-class products, first-class reputation, and first-class professional services.
■ Guide Installation and Cold and Hot Commissioning Services
We will provide guidance on installation and cold and hot debugging services for users who purchase our company's products, ensuring that the equipment operates in the best state.
■ Technical Training
We provide professional skill training for users' equipment operators and maintenance personnel. Senior engineers explain the structure, working principle, functions of various components, use of professional tools, maintenance and debugging steps, and common problems encountered during maintenance to user personnel, enabling them to better inspect and maintain products.
■ Telephone Duty Service
We have opened a 24-hour duty hotline to provide users with answers to problems encountered during equipment operation. Professional personnel will arrive at the site within 48 hours after receiving the user's request fax to provide on-site service.
Professional Level A, B, C, and D Maintenance Services for Soot Blowers
Provide users with equipment disassembly and maintenance services during maintenance services, including planned maintenance during major, medium, and minor repairs. Due to the company having an experienced and technically comprehensive professional maintenance team, after professional personnel's maintenance, the user's equipment is restored to its intact state, and online operation is more stable and reliable, extending the equipment's lifespan.
The company has a comprehensive service management system, with numerous professional technical personnel and a well-trained and experienced technical team. Each service personnel in the team possesses professional and independent technical capabilities, with years of work experience and industry background. At the same time, the company provides various skill training for technical service personnel according to the requirements of product technical support, and provides comprehensive, extensive, and comprehensive services and reliable technical support to users at any time.
Scope of maintenance services:
Special adjustment and inspection, preventive inspection, testing, refueling, and maintenance work for the normal operation of all equipment and the integrity or restoration of components in the system, including all equipment within the system such as the main body, pipelines, and program control.
We have received unanimous praise and affirmation from our users, both in terms of technical level, service quality, and reasonable fees. Every employee of the company will adhere to the service philosophy of "professionalism, economy, and efficiency" to provide users with high-quality and comprehensive services.
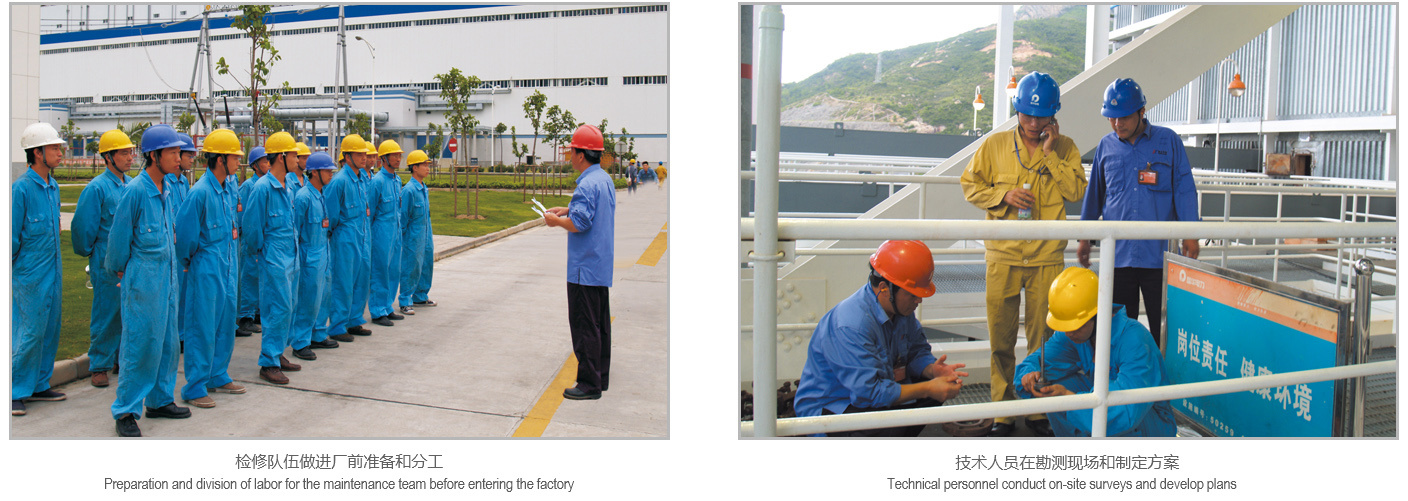
Fully Supported On-site Maintenance Services
How to use the soot blower correctly and improve its operation rate, so as to play a normal role in the safe and economic operation of the boiler, has become a highly concerned issue for users. Our company provides comprehensive services in the form of annual large packages to customers through the full support on-site service. All daily maintenance, operation, and unplanned shutdown maintenance of the soot blowing system, as well as a series of on-site work, will be completed by our company's professional service team, forming a continuity of professional services and relieving users of the worries caused by the passive elimination of equipment division of labor and operation.
Based on years of on-site practical experience, a systematic and optimal daily maintenance and operation plan has been developed for each specific project, improving the equipment operation rate and optimal usage effect. The localized service of imported equipment has been successfully solved. Due to the correct use and timely elimination of defects of the equipment, the best soot blowing effect has been achieved with minimal steam consumption, thereby improving the thermal efficiency of the boiler. To save operating costs for users and truly achieve the goals of safe, efficient, and economical operation of boilers.
Through this professional and meticulous daily maintenance service, the normal operation of the equipment is ensured, enabling the soot blowing system to maximize economic benefits. Reduce and eliminate various losses caused by faults in the soot blowing system.
The service content includes:
Daily and regular adjustment and testing, preventive testing, testing, defect elimination, lubrication, disassembly, maintenance and replacement, as well as random operation, on-site tracking and monitoring, and operation status recovery, are carried out to ensure the normal operation of all equipment in the system and the integrity or restoration of components and constructions, including unplanned maintenance and temporary repairs. The majors involved include electrical, thermal, piping, and mechanical.
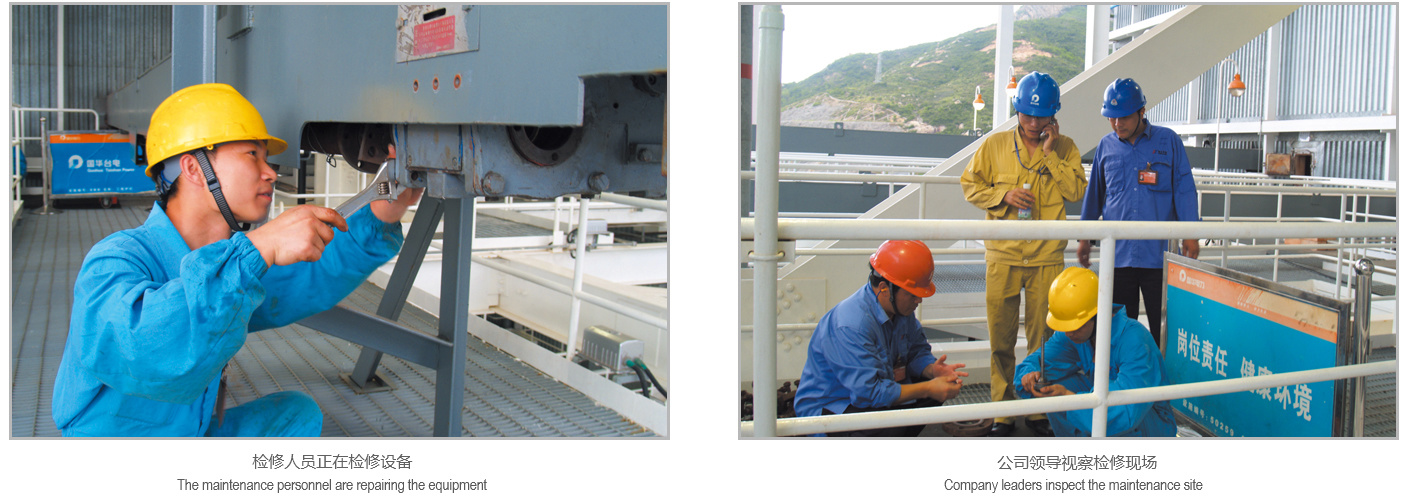